Temperature control units
Temperature control units
Temperature control units keep the temperature of the mold at the desired level. This can be relatively cold (+/- 30 °C) to very hot (+/- 300°C), depending entirely on what the process requires. The set temperature is reached and maintained by means of heating and cooling.
There are different versions possible:
- Direct cooling (the cooling water is also used to temper the mold temperature.
- Indirect cooling (cooling is achieved by means of a heat exchanger)
- Water pressure temperature controllers (for temperatures up to 160°C)
- Oil tempering equipment
The Marse tempering devices are distinguished as follows:
- German Speck pumps, Austrian Sigmatek touchscreen
- Swedish Swep heat exchangers
- General Electric components
- Industry 4.0 communication protocols
- Precise PID temperature control
- Choice of different pumps incl. suction function
- Stainless steel tank and heater
- Leakage monitoring
- Security sensor present
- Standard (cooled) solid state relays
Brochure/contact request
Leave your details and receive the Temperature control units brochure.
RequestTemperature control units
It is important that the right capacity temperature device fits the requirements of the process. Pump capacity, temperature, cooling capacity, heating capacity, pressure, etc.
Marse works with 2 versions of the tempering devices.
- Push button operation (budget version)
- Touchscreen (premium version)
The touchscreen version responds to the wishes/requirements of the 4.0 industry.
- Various interfaces: TTY 20mA, RS485, RS232, Ethernet, OPC UA
- Temperature graphs
- Volume flow insight into regulation
- Additional temperature display in return
- Pressure monitoring
- Digital input and output signals
- Analog signals/ output 4-20mA
- Optional profinet, modbus, etc.
- Memory function for different dies
- Alarm history
- Acoustic alarm
Marse
Marse is a manufacturer of equipment and machinery for the plastics processing industry, chemical industry and pharmaceutical industry. The company was founded in 1978 and has a clear mission: to provide the best customer service, focusing on the highest quality and reliability of the products.
In 1998, the 2nd generation took over and an international expansion was made, accompanied by a modernization of the product portfolio. In 2017, there was a major expansion of the facility and staff. In addition, the products were improved again and work procedures optimized. All these years, the values and philosophy have been preserved to deliver the best possible products to the industry.
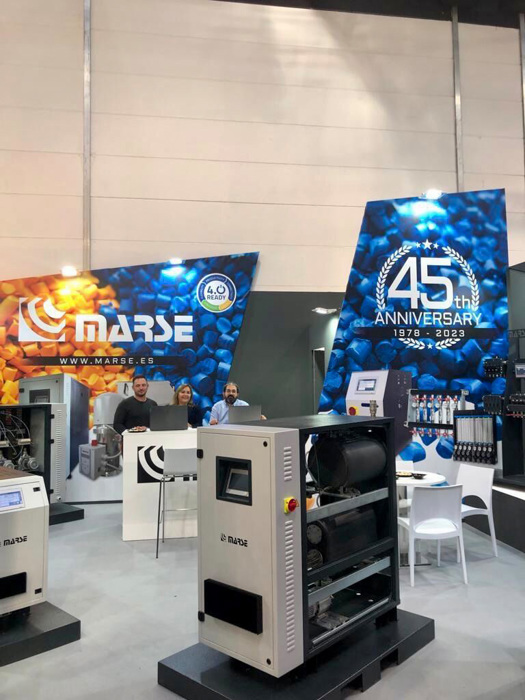
Temperature control units
Leave your details and we will send you the brochure about Temperature control units as soon as possible.
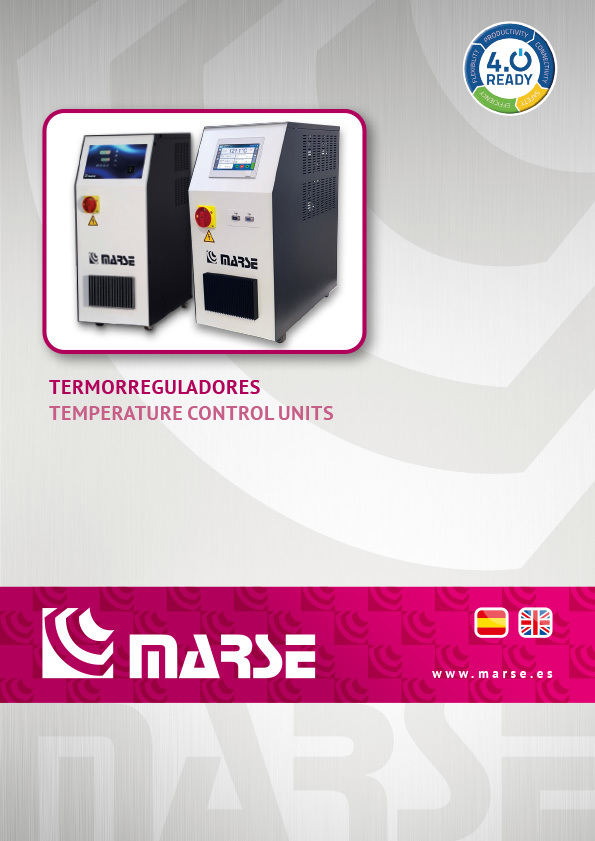